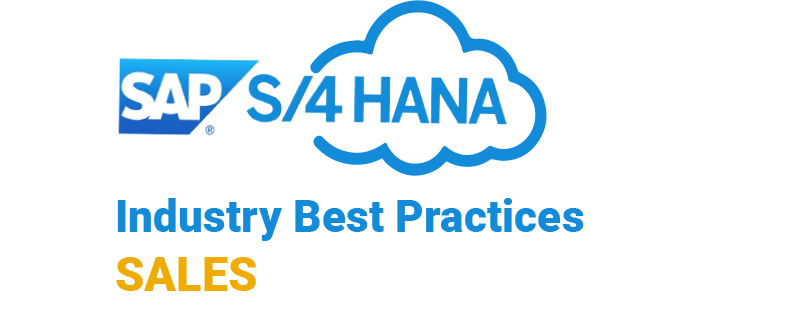
Delivery Processing without Order Reference (1MI)
If the relevant master data has been previously maintained (for example, Business Partner for Customer), the process starts when a standard delivery is created. Based on this delivery document, picking slips are generated to stage the product for shipment to the customer.
If a delivery includes batch managed materials, a batch number can be entered for each delivery item. If the required quantity is delivered using pieces belonging to different batches, original delivery items can be split to enable proper recording of delivered quantities for each actual batch.
The delivery document can be split into two or more deliveries, for example, to accommodate late changes in transportation planning. In addition, freight costs can be added to the delivery documents to ensure that these costs are taken into account for invoicing.
After picking is complete, the shipping specialist relieves the inventory by posting a goods issue. This inventory relief is the actual recording of the physical quantity that is being shipped to the customer. The cost of goods sold is then recorded in financial accounting.
Once the inventory is relieved, the delivery can be invoiced. If the master data of the customer or ship-to party involved states that a proof-of-delivery is required, the quantity delivered must be confirmed by the customer. Once this confirmation is maintained for each delivery document, invoicing (fully based on the confirmed quantities) can be carried out. The revenue and the cost of goods sold is then also recorded in management accounting.
Key Process Steps Covered
- Create delivery
- Create attachment for delivery
- Execute picking
- Enter batch number
- Split outbound delivery
- Add freight costs
- Posting goods issue
- Proof of delivery
- Create billing document
Benefits
- Enable customers to:
- Pick goods from manufacturer’s warehouse without advance order
- Directly pick, pack, and send
- Receive goods for review without order
Where is Delivery Processing without Order Reference(1MI) being used?
This Scope item is used in the following way:
- As a core function of Order and Contract Management within Sales Scope Item Group